Residual stresses and strains in metal additive manufacturing
Master thesis- Axis:
- Structures et matériaux innovants
- Site :
- Lille
- Type:
- Master thesis
- Supervising person(s):
- Anne Mouftiez
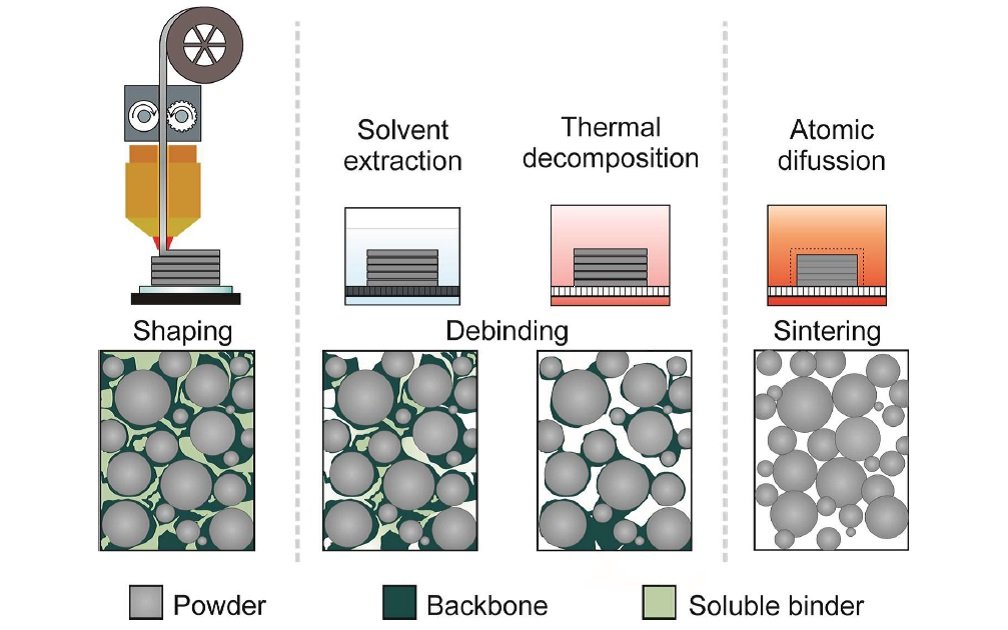
Background :
Fused filament fabrication can be used for metal additive manufacturing according to the following process. The part is shaped by extrusion of a composite wire made of metal particles embedded in a polymer matrix. The so called green shaped is debinded, meaning the polymer matrix is removed. Then the metal particles are sintered, which produces a contraction that roughly represents 1/3 of the starting volume.
One of the major issues in additive manufacturing of metal parts is to produce parts with accurate size and dimensions. Although the in-plane displacements of the manufacturing tools (extrusion heads, nozzles for deposition and electron or laser guns) are well controlled and the size of the seams is very small, the large temperature variations that locally occur during the process generate changes in volume of the material which in turn produce residual stresses. The latter especially in one step melting processes (selective melting and deposition), may lead to large strains or even cracks in the manufactured parts.
Issue
In two step processes which use sintering in order to consolidate the metal part, residual stresses or strains are not expected to occur the same way since the material phase that has suffered the extrusion process is removed during debinding. However, experiments made at ICAM show that some distorsions in geometry are produced during the whole process. In order to elucidate the mechanisms of such deformations, both steps of the process need to be investigated.
- First sintering, and its consequences on residual stresses and strains in parts produced out of one single material on one hand and out of two materials (metal particles and the ceramic particles that are used as scaffolding in the additive manufacturing process).
- Next extrusion of composite wires. As a matter of fact, if the seams do not exactly follow the planned deposition scheme, metal particle density may vary from expectations and deformations be produced.
Work program
Both processes have to be documented by litterature review. Experiments are to be performed on a Markforged machine which does not enable to change extrusion parameters. So it is proposed to look into this issue by manufacturing parts with the same geometry but different building paths. These parts also have to support manufacturing with and without interfaces with scaffolding material. Lastly, the parts should be manufactured out of two different metal alloys, one of which being a tool steel that is subject to rather large changes in volume during heat treatment. The experiments will be designed as a sequel of a previous study started during the first semester of 2020.
The materials used in the building wires will be characterized, and so will be the microstructure of the parts, at every step of the manufacturing process (microhardness, optical and scanning electron microscopy). Residual stress analysis will be performed in colllaboration with LGEEM (IUT A, Villeneuve d’Ascq) using a proto XRD device.
- required skills:
-
The applicants should have skills in materials science (being trained in metallography would be an asset), and in CAD at least. Being able to use FEM software to model displacements, strains and stresses occurring during the process would be appreciated.