Comparison of corrosion resistance between alloys elaborated with metal additive manufacturing and classical metallurgy
Master thesis- Axis:
- Site :
- Toulouse
- Type:
- Master thesis
- Supervising person(s):
- Sophie Régnier
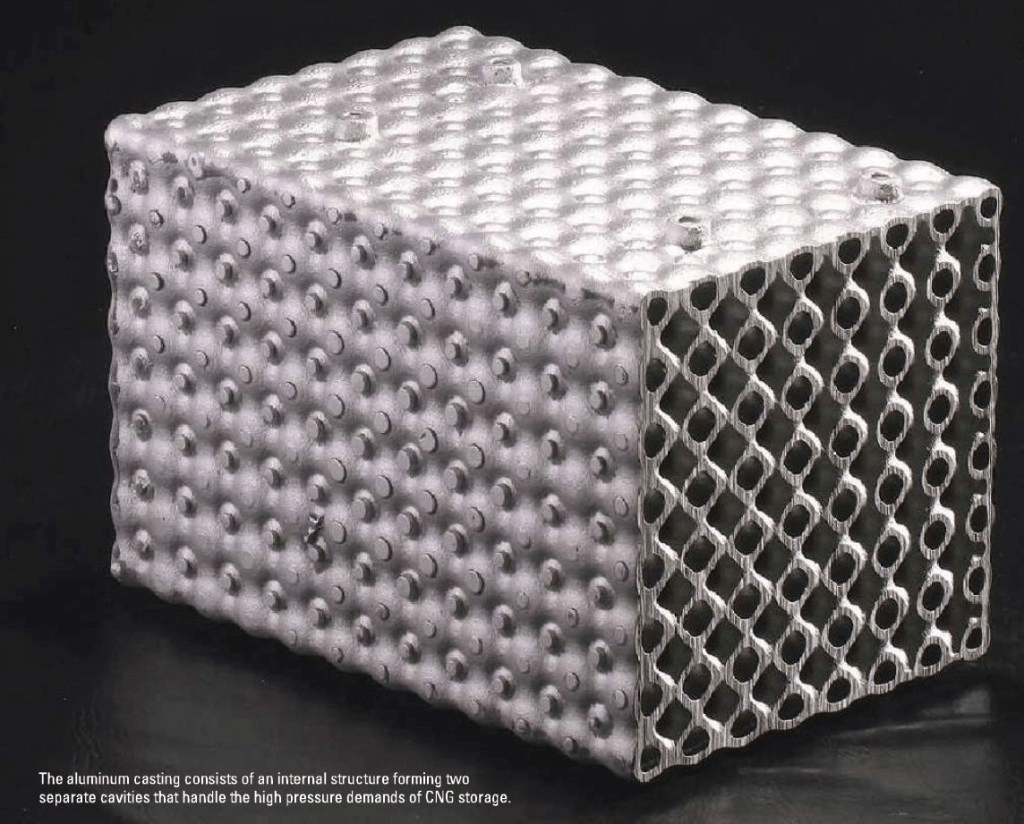
Background :
For many years, metallic materials are manufacturing by classical metallurgical processes. The properties of the alloys so manufactured have been tested many times and are today often well known.
For a few time, new industrial processes permit the development of metallic materials. These are processes using Additive Layer Manufacturing, as Laser Powder Bed Melting Manufacturing, Electron Beams Manufacturing.
These new elaborating processes have several advantages like the direct way to obtain near finished metal pieces, the possible manufacturing of complex forms, But, there are some disadvantages, like the time of the manufacturing, the post highlighting of defects (as unmelting part of powder, porosity, non homogeneous mixing of two successive melting layers, roughness,…). Today, many research studies concern the ways to decrease the quantity of these surface defects directly during the process. Other actual research works present some characterizations of residual stresses, mechanical properties, … But there is only a few result concerning the corrosion resistance of such samples.
Aim of the study :
The pieces manufactured by ALM present a surface with some imperfections or defects. It would be interesting to know the effect of these defects on the corrosion properties of such pieces. A comparison would be made with samples manufactured with classical manufacturing and surface preparation machining.
Work program :
These relatively new ALM processes and the impact of this type of manufacturing on the surface properties as corrosion resistance have to be documented by literature review.
The tested alloys would be aluminum based alloys (Al-Cu, Al-Zn) and Titanium based alloy (TiAlV).
Before corrosion tests, the samples should have to be observed with optical microscopy and SEM to visualize the type of present defects and to quantify them. Tests such as roughness measurements and other surface characterization (microhardness,..) should be performed.
Concerning the comparative corrosion resistance between ALM samples and classical metallurgy samples, experiments should be performed with stationary mode and nonstationary mode. The electrolyte would be determined due to the type and the quantity of surface defects and the bibliography results.
- required skills:
-
The applicants should have skills in materials science, especially metallic materials. Being interested with experiment and test development would be appreciate on one side and the analysis of experimental results on the other side.